
Vishal Dahiya on how Panasonic aims to enable manufacturers for Industry 4.0 with smart factory solutions
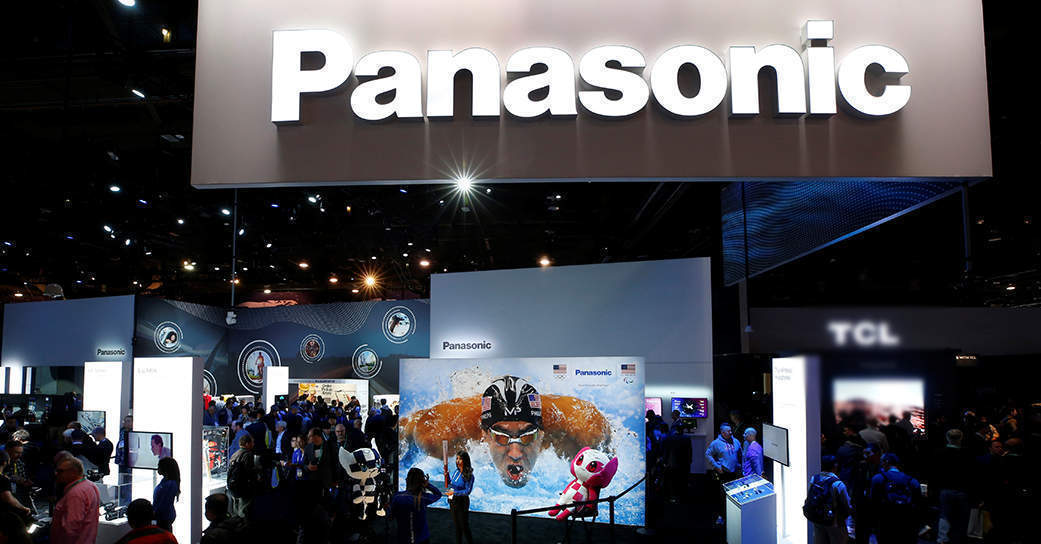

In April last year, Japanese consumer electronics major Panasonic set the ball rolling on ramping up its smart factory solutions business in India. By 2022, the company expects to generate upto Rs 1,000 crore in revenues from the business via the delivery of smart solutions and services along with world class hardware to the manufacturing industry.
The company said, at the time, that it would focus on building India as its innovation hub for the globe, and create a strong ecosystem of component and automated manufacturing in the country. Panasonic’s smart factory solutions push in India aims to capitalise on the Industry 4.0 wave that encompasses a line of solutions that integrate wireless connectivity, sensors and connected systems to help manufacturers visualise the entire production line.
In an interview with TechCircle, Vishal Dahiya, head, Panasonic Smart Factory Solutions India, spoke about how the company is building out its smart factory solutions business in the country.

Edited excerpts:
Tell us more about how Panasonic is building out its smart factory solutions capabilities here.
We are on the cusp of the next industrial revolution and smart factories are going to be at the core of how manufacturing evolves in the future.

Panasonic is known for providing end-to-end solutions to consumers and businesses alike and when we look at Industry 4.0, we know we are well poised to be a key player in this space.
This is one of the major reasons why we decided to integrate our welding business and SMT (surface mount technology) equipment business to consolidate our software and hardware capabilities and become an end-to-end integrated smart manufacturing solutions company.

Our current smart factory offering comprises various solutions that cater to different business needs. For instance, iLNB (integrated line management system) integrates all equipment in PCBA (assembly of printed circuit board) process line to get real time data and control. iLNB can help automate up to 70-80% of the manual processes. We have OEE (overall equipment efficiency) visualisation solutions for management to visualise their factories. This bridges the gap between them and the production floor, resulting in quick response time and decision making. Similarly, we use ‘asprova’ as a solution for production planning, I-reporter to capture manual data digitally and motion board for data visualisation.
What kind of benefits do you expect to derive from this business in the long term?
Our aim is to be enablers for India to be at the helm of the next industrial wave. The benefits that we are looking at are not only growth-oriented but also value based for our customers. The smart factory solutions that we are offering will help sectors streamline their manufacturing processes, improve efficiencies and increase productivity.
This will have its own benefits which help contribute to the larger business goals that we have in place. Our revenue target from smart factory business is Rs 1,000 crore (by 2022). Solutions and digital manufacturing will form 15% of our smart factory business.
Who would be the typical customers for your smart factory solutions?

We are looking to target manufacturers across the board. Anyone who is looking to build manufacturing capabilities for Industry 4.0 can benefit from our smart factory solutions. The primary sectors that can use our current solutions include automobiles, smartphones, energy meters, etc. The mobile and ICT manufacturing industries present tremendous opportunities to us.
Could you elaborate on iLNB and how it helps automate manufacturing processes? How will the production cycle be impacted by iLNB's implementation?
With iLNB manufacturers can control the entire machinery infrastructure through one single system. One would just need a remote control centre to view and collect information on production, the state of machinery and so on. With iLNB, manufacturers today can control the entire PCBA (SMT) line to collect valuable data and increase overall productivity. It further helps them assist with automatic changeover in a line and thus reducing setup loss and labour costs.

We have established one single line of communication for the entire setup, which helps reduce manual processes up to 80%, thus saving time and improving production.
What about the impact on inventory cycles and manual workforces?
While smart factory solutions will redefine how the manual workforce at factories perform their jobs, the impact will be positive. In order to efficiently manage the smart factories, there are new roles that will be developed with requirements for technical skills that are befitting of the next industrial wave.
Organisations that use smart manufacturing can benefit from the increase in revenues that the technology will bring to expand their business, thus creating requirements for new hires.

Areas such as electronics, cyber security and so on will see a spike in the jobs, resulting in various new profiles as opposed to the traditional way of manufacturing.
By employing a smart warehouse management system, we can effectively control the inward and outward inventory cycle. Manufacturers make can capture real-time data and minimize the downtime to improve their production planning.
Take us through some real world use cases of these smart factory solutions.
At Panasonic, we have several use cases demonstrating our efficiencies. For one of our automotive customers, we used our solutions to capture the moulding machine status and production process data in order to display the OEE (overall equipment efficiency) of each machine. This helped them take timely corrective action thereby, increasing the overall efficiencies.
In case of other equipment manufacturers, we deployed our energy management system to help cut the power losses which in turn resulted in improving the bottom line.
One of the established instrument manufacturers in the country used our solution to digitize their entire manual reporting. It further helped them in effective, quality data management and collection of real time information.
Similarly, for one of the component makers, our smart factory solution for production planning and control has helped them improve their overall productivity and thereby, improving their delivery commitments to end customers.